WPC (Wood-Plastic Composite) wall panels have gained popularity in the construction industry due to their durability, versatility, and eco-friendly nature.
To appreciate the qualities of WPC wall panels, it is crucial to understand their manufacturing process.
In this article, we will delve into the various stages involved in producing WPC wall panels, from material selection to final product assembly.
Understanding the manufacturing process will shed light on the efforts and expertise of manufacturers, suppliers, and factories in creating high-quality WPC wall panels.
Material Selection and Preparation
The first step in manufacturing WPC wall panels is selecting suitable materials.
Manufacturers typically use a combination of wood fibers or flour and thermoplastics, such as polyethylene or polypropylene.
The wood fibers provide strength, while the thermoplastics offer durability and flexibility.
During the preparation stage, the wood fibers and thermoplastics are carefully blended, ensuring proper distribution and adherence of the materials.
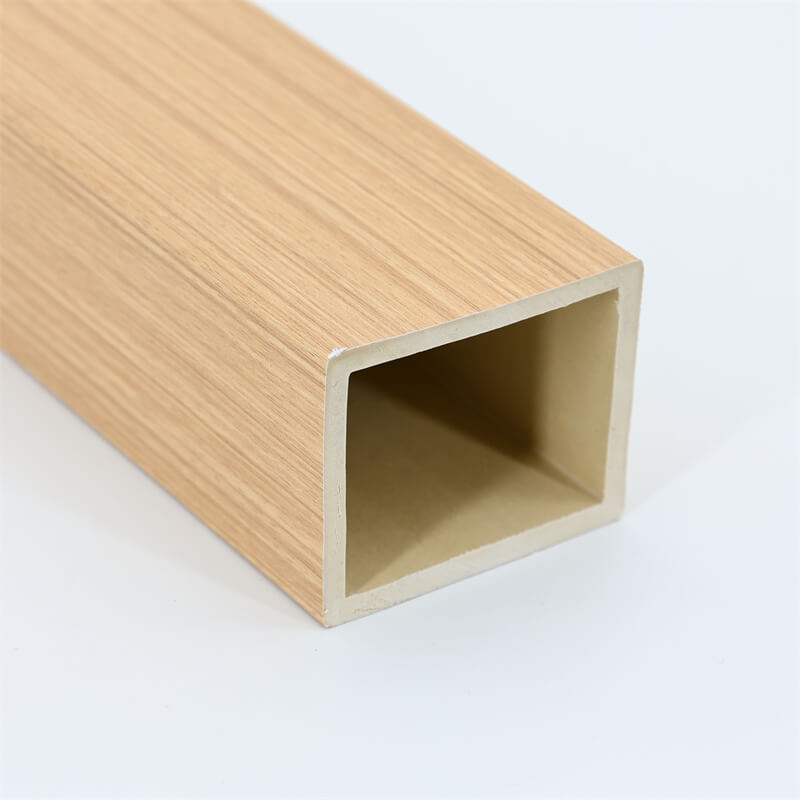
Extrusion Process
The extrusion process is a key stage in the manufacturing of WPC wall panels.
In this process, the blended material is fed into an extruder, which melts and homogenizes the mixture.
The molten material is then forced through a die, giving it the desired shape and size.
Cooling is applied to solidify the extruded material, resulting in a solid panel with consistent dimensions.
Manufacturers can customize the extrusion process to achieve specific design features, such as grooves or patterns on the surface of the panels.
Surface Treatment and Finishing
After extrusion, the WPC wall panels undergo surface treatment and finishing.
This stage involves several processes to enhance the appearance, durability, and weather resistance of the panels.
Surface treatment may include sanding, embossing, or brushing to create desired textures or patterns.
Finishing options range from applying coatings, such as paints or stains, to improve aesthetics and protect the panels from environmental elements.
The choice of finish can vary depending on the desired appearance, whether it is a natural wood grain or a vibrant color.
Quality Control and Assembly
Before reaching the market, manufacturers conduct rigorous quality control measures to ensure the production of high-quality WPC wall panels.
This includes checking the dimensions, strength, and visual aspects of the panels.
Any defective or substandard panels are discarded to maintain consistent quality standards.
Once the quality control process is complete, the panels are ready for assembly and packaging.
Manufacturers may provide additional services, such as custom cutting or edge treatments, to meet specific customer requirements.
Understanding the manufacturing process of WPC wall panels provides valuable insights into the efforts and expertise involved in creating these versatile construction materials.
From material selection to final product assembly, manufacturers, suppliers, and factories play a crucial role in producing high-quality WPC wall panels.
The meticulous selection and preparation of materials, the extrusion process, surface treatment, and finishing all contribute to the durability, aesthetics, and functionality of the panels.
Additionally, thorough quality control measures ensure that customers receive reliable and consistent products.
By comprehending the manufacturing process, individuals can appreciate the intricate craftsmanship behind WPC wall panels and make informed decisions when purchasing these sustainable and versatile construction materials.